Scott & Carol Present: Getting On Track With B&M
When you ride a coaster designed by Bolliger and Mabillard, do you ever wonder how the track is made? Or do you think it just magically appears in the staging area to be assembled? One track builder B & M use is located in southwestern Ohio. Here is an inside look for News Plus Notes readers about this fascinating process. Our tour guide for today is Ken Miller, the General Manager of the plant. He has spent his entire career at the facility, starting by sweeping the floors. He took us through the over 152,000 square foot steel fabricating facility.

“It all started back in 1989 when Walter Bolliger came to my office and asked if we would be interested in building track for their company,” said Miller. “They had seen some of our work on the supports for the Arrow coaster at Kings Island, (Vortex,) and Six Flags Great America, (Shockwave,) and liked what they saw. Now they keep us busy seven days a week with all their projects. Every piece of track for every one of their roller coasters in the United States is made right here in Ohio.”

The track begins as flat sheets of steel and pipe for the support columns is sourced in the United States. The bent pieces of track pipe are brought in from Europe. Most B & M coasters are custom designed. Each track element is a compilation of different sequences and requires a lot of flexibility of the workshop.

So let’s start with the support columns. Every piece of pipe used in making the support columns is hand cut by one of the seventy-nine employees at the factory. “The process used to start with blue prints, “Miller says, “but now it is mainly XYZ coordinates. The use of digital transmission for product specifications has made blueprints obsolete. We also send all of our quality control data back to them electronically. The results of every test are all kept on file by both us and B & M.


The flanges for the columns are cut using a CNC oxi cutter because they are made from over one and one half inch thick steel plate. They have cutters with either a 20’ or 40’ table. The plates are then sent out to be machined to the final measurements. When they return, the flanges are welded onto the pipe. According to Miller, “Our Quality Control department's nondestructive testing personnel are certified to the guidelines of the American Society for Nondestructive Testing (ASNT). We do a magnetic particle test or ultrasonic test on every weld, depending on B & M’s requirements.

After being machined to final dimensions, the supports are processed and painted before shipping. The paint inspectors are certified to ensure consistent quality for all customer requirements. No this photo isn’t of supports, but it was the only thing they were painting on the day we were there. Any guess where these pieces are going?
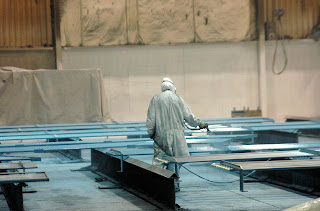
All of the columns have an extension that projects down into the empty space on the concrete footer. Large nuts and washers are used to adjust the height and angle of the support to get them in the correct position. After the track is bolted on the support, the hole in the footer is filled with concrete so more than just the bolts support the various stresses put on the column. Every year, every nut is torque tested and a paint mark used to make sure it has not loosened during seasonal operations. According to Mr. Miller, when they have moved their coasters, the only things that changed were the supports. Nothing was changed on the track itself.
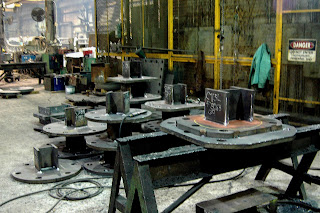
If you have followed the evolution of B & M track, you remember how it used to have ball and socket joints on the bottom of track pieces to facilitate the installation process. Now the steel fabricator has tightened the tolerances to within one millimeter for all measurements. This has eliminated the need for the joints and also eliminated the need for the customer to continue lubricating those joints for the life of the roller coaster. While this seems like a small thing, coasters can last for a long time if properly maintained so customers really appreciate any small savings that continue to add up year after year.

When we all saw our first coaster from Bolliger and Mabillard, it was very distinctive. The square box track was all the same size, and it appeared to be made from lots of small triangles. Now they have many different sizes of track, depending on the type of coaster being made for that specific project. Here are some samples of the various kinds of B & M track. The track for their first coaster, Iron Wolf at Six Flags Great America looks very similar to the track for Batman: the ride at the same park. The increase in weight of the flying coaster cars necessitated thicker tubes and a larger box. And when they introduced the dive coaster, the track and support structure took another jump is size.


Ken Miller did not allow us to see the manufacturing process of the track. Obviously, it is a very precise process that B&M wants to keep secret. Here are a few pictures we were able to take.




It takes about a week for an individual element to be completed, and usually they have many in production. “Once we get the production line full, we can crank out nearly fifteen elements per week,” says Miller. No element is sent for painting, until QC signs off on each element. Once the piece is approved, it goes through the same painting process as a support column.



But the attention to detail does not stop at the plant. Since the pieces of track are kept to very close tolerances, any dings that occur during transport and assembly could cause a problem during assembly. As an extra precaution, they even have end caps made to protect the ends of the track during transport and assembly. Of course they don’t paint them, but it is an effective demonstration of the lengths they go to striving for the “perfect” coaster. The elements are bar coded before being loaded onto a trailer.

Miller continues, “We usually can get two to three elements onto a trailer. We did have to change the bar code stickers because some coaster enthusiasts started taking pictures of them and posting them on the internet before the park had made their announcement. No more identifying information is on the bar codes.”
Once the track leaves the plant it usually is off loaded at a staging area at the park. The bar codes help identify which piece is next for the assembly process. You don’t want to bring in the last piece you need early in the process, where it can get scratched or damaged. The bar codes also list the weight of the element, which is useful to both the crane operator and the trailer loader.


So now you know as much as they publicly want you to know, and for many of you, it is much more than you ever cared to read about. But when you’re standing in line for that next ride on one of their coasters, we hope you can remember a couple of things you found interesting in this article. So thanks for reading stay warm until next time.
9 comments:
THANK YOU! This was awesome.
Yes thank you very much for putting this on!!!!!!
Thanks guys, all credit goes to Scott & Carol.
Please feel free to spread the word about this exclusive!
Any idea at all what coaster was being worked on while you were there? At any point did Carol distract Ken Miller so that Scott could sneak off and get us some coaster intell?
Great post NewsPlusNotes!
Scott & Carol don't coaster kiss-and-tell! :)
Really, though, it took an immense amount of effort and trust to get that tour to happen (again all credit to Scott & Carol for that) so even I have no idea about those details!
I think that its pretty funny that they mentioned that little bit about Coaster Enthusiasts taking pictures of bar codes and foiling their plans!
I can see B&M and that factory just shaking their fists and saying "Damn you coaster enthusiasts!"
Thank you
Great work as always kids...maybe we'll get to meet up and check out the new Beemer in Cincy sometime this year, huh?
This is great! Very interesting! I'm curious, if the track is different for each type of coaster, is it possible to switch the type of trains on it? Like switching stand-up trains for floorless ones?
Post a Comment